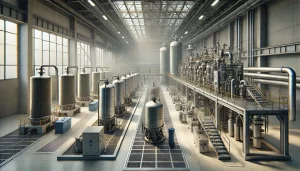
26
Nov
Understanding the Different Types of Oil Filter Materials: A Comparison of Synthetic vs. Natural Fibers
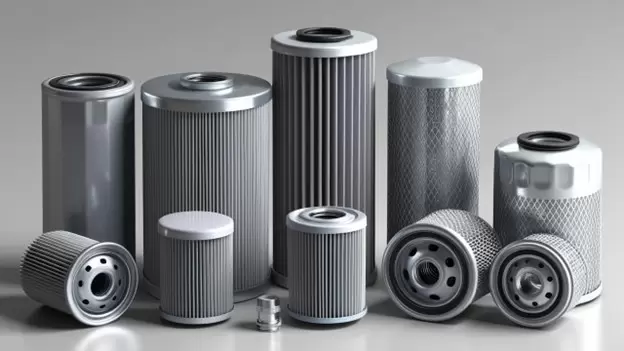
In industrial applications, maintaining clean oil is essential for maximizing equipment performance, extending oil life, and reducing machinery wear. Oil filters play a crucial role in this process by removing contaminants through mechanisms like depth filtration and pleated filters, which enhance dirt holding capacity. The materials used in filter inserts, whether synthetic or natural, directly impact filtration efficiency, durability, and environmental impact. This article compares synthetic and natural fiber filters, with a focus on the evolving preference for sustainable options like cellulose-based filter inserts.
Why Filter Material Matters
The choice of filter material affects not only the filtration performance but also the filter’s durability and contamination capacity. Effective filtration requires materials that capture particles efficiently without causing excessive restriction, which could reduce oil flow and impact machinery efficiency. Depth filtration and pleated filters are often used to optimize dirt holding capacity and extend filter life.
Synthetic Fibers: High Performance with Environmental Drawbacks
Benefits of Synthetic Fiber Filters
- High Durability: Synthetic fibers withstand high pressure and temperature, making them suitable for demanding applications where durability and high contamination capacity are crucial.
- Reliable Depth Filtration: Synthetic filters are precisely manufactured, ensuring consistent pore sizes that enhance dirt holding capacity and enable reliable depth filtration for extended use.
- Longer Filter Life: Due to their robust construction, synthetic filters often need fewer replacements, reducing downtime and maintenance costs.
Drawbacks of Synthetic Fiber Filters
- Environmental Concerns: Derived from non-renewable resources, synthetic fibers are not biodegradable and contribute to landfill waste. Their production also has a high carbon footprint.
Trending Insights
Products Categories
- Limited Applications: Certain industries prefer natural filters for compatibility and sustainability reasons. Additionally, synthetic filters may introduce unwanted chemicals into sensitive systems.
- Higher Costs: High-performance synthetic fibers such as fiberglass can be costly, impacting budget-conscious applications.
While synthetic fiber filters are known for their durability and contamination capacity, their environmental impact and production costs have led to an increasing interest in sustainable, natural alternatives.
Natural Fibers: Sustainable and Effective Filtration
Benefits of Natural Fiber Filters
- Sustainability: Derived from renewable sources, cellulose filter inserts are fully biodegradable and free from metals, plastics, or chemical additives, reducing their environmental impact.
- Enhanced Particle Capture: Cellulose fibers, due to their natural structure, offer varied shapes and sizes, creating a matrix that effectively captures a wide range of particles. This structure supports depth filtration and enhances dirt holding capacity, helping keep oil cleaner for longer.
- Chemical-Free: Natural fiber filters, made without chemicals or plastics, reduce the risk of chemical leaching, ensuring a cleaner filtration process that maintains oil purity.
Drawbacks of Natural Fiber Filters
- Limited Durability: In certain high-temperature or high-pressure environments, natural fibers may not match the durability of synthetic materials, though advancements are continuously improving their performance.
- Replacement Frequency: While natural filters excel in dirt holding capacity, they may require more frequent replacement in certain high-demand applications.
- Compatibility: Cellulose-based filter inserts may not suit every application; particularly where ultra-precise filtration is required. However, they are a practical choice for industries prioritizing sustainability and lower environmental impact.
Filtration Efficiency and Performance
Both synthetic and natural fiber filters offer strong filtration capabilities, but their structural differences affect depth filtration and dirt holding capacity. Synthetic filters, often designed as pleated filters, provide consistent pore sizes, making them ideal for applications needing precise filtration. However, the irregular, varied structure of cellulose fibers supports effective depth filtration, allowing for a broader range of particle sizes to be captured, enhancing the contamination capacity.
Natural fibers like cellulose often provide filtration results similar to synthetic options but without added chemicals, which supports cleaner oil and extends machinery life. For many industries, this combination of performance and sustainability makes cellulose filters an attractive option.
Environmental Impact: The Case for Natural Fibers
As industries adopt greener practices, the demand for sustainable filtration solutions has increased. Synthetic filters, although effective, contribute to landfill waste and are derived from non-renewable resources. Their non-biodegradable nature means they remain in landfills long after disposal.
In contrast, cellulose fiber filter inserts offer a fully biodegradable alternative. Their natural origin and compatibility with various filtration methods, including depth filtration, reduce environmental impact. Companies transitioning toward environmentally responsible practices often choose natural fiber filters to meet their sustainability goals, without sacrificing performance or contamination capacity.
Selecting the Right Filter Material
The ideal choice of filter material depends on operational needs, environmental considerations, and industry standards. Synthetic fibers are valuable for applications demanding high contamination capacity, durability, and precision filtration. However, cellulose filter inserts are gaining popularity for their eco-friendly properties, cost-effectiveness, and strong depth filtration performance.
For industries looking to align with sustainability goals while maintaining effective oil filtration, cellulose fiber filters offer a viable alternative to synthetics. They capture contaminants efficiently, extend oil life, and contribute to a cleaner planet—a solution that modern industries can embrace.
Conclusion
The choice between synthetic and natural fiber filter inserts depends on specific application requirements and sustainability objectives. Synthetic fibers deliver reliable durability and high contamination capacity, particularly in extreme environments. However, natural cellulose fibers provide biodegradable, high-performance options that align with environmental initiatives. As industries shift towards sustainable practices, cellulose-based filter inserts represent a promising solution, balancing performance with environmental responsibility.