
24
Oct
Mini Boosters and Safety: Enhancing System Reliability in High-Pressure Environments
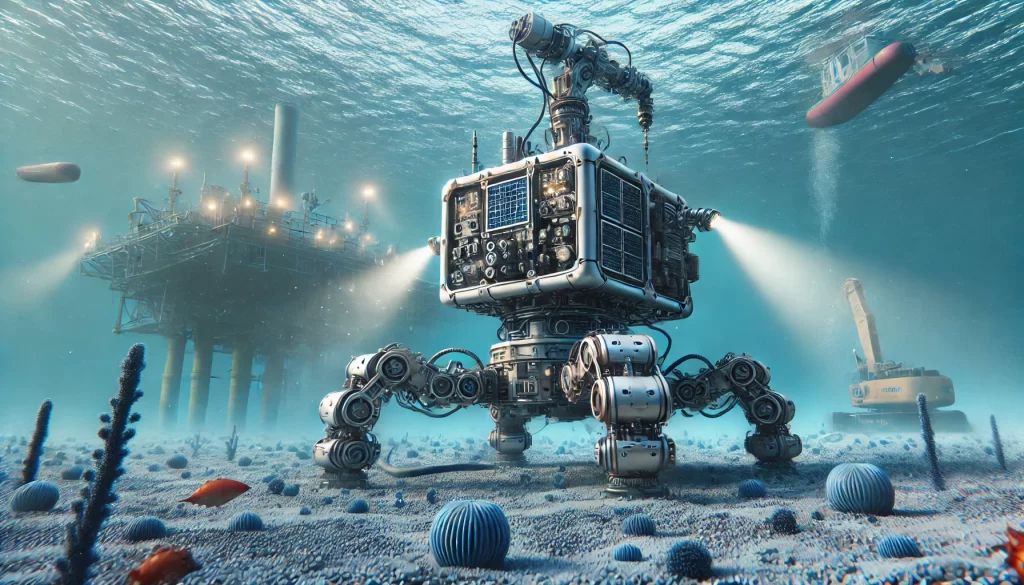
In high-pressure hydraulic systems, safety and reliability are of paramount importance. These precision hydraulics systems, commonly found in industries like aerospace, automotive, oil and gas, and heavy machinery, operate under intense pressure and require exact control to function efficiently. Mini boosters, small yet powerful pressure amplifiers, have emerged as a crucial component in enhancing the safety and performance of these hydraulic systems.
In this article, we will delve into the critical role of mini boosters in hydraulics engineering, examine the common safety challenges in high-pressure environments, and explore how miniboosters improve system reliability and safety.
The Role of Mini Boosters in High Pressure Hydraulic Systems
A mini booster is a hydraulic pressure amplifier designed to increase the pressure of hydraulic fluids in a compact and efficient manner. In hydraulics engineering systems where high pressure operation is essential, such as in heavy machinery or precision hydraulics, mini boosters provide an elegant solution to amplify fluid pressure without requiring larger, more complex components.
Mini boosters function on Pascal’s law, which states that pressure applied to a confined fluid is transmitted equally in all directions. This fundamental principle allows the device to boost hydraulic pressure by utilizing a hydraulic piston and cylinder setup. When the fluid enters the mini booster, it exerts pressure on the piston, which is then transferred to the cylinder, resulting in amplified pressure that can be used for various high pressure environments.
Mini boosters can operate in a wide temperature range, from -30°C to 100°C (-22°F to 212°F), depending on the seals and materials used. This makes them suitable for extreme environmental conditions.
In industries where reliability and safety are critical, mini boosters provide a compact solution for achieving high-pressure outputs while minimizing the need for large, space-consuming hydraulic systems. Applications such as injection molding, forging, and aerospace manufacturing rely on the efficiency of mini boosters to ensure stable operations in high-pressure environments
Common Safety Challenges in High-Pressure Environments
High pressure hydraulic systems present unique safety challenges.
Trending Insights
Products Categories
Components within these systems are exposed to extreme forces, and even minor malfunctions can lead to catastrophic failures. Some of the most common safety challenges include:
Stress-Induced Failures:
Hydraulic components are subjected to high levels of stress, which can lead to fatigue and wear over time. This can result in leaks, ruptures, or even complete system failure if not properly managed.
Pressure Spikes:
Sudden increases in hydraulic pressure, known as pressure spikes, are a common occurrence in high-pressure systems. These spikes can cause damage to valves, hoses, seals, and other components, potentially leading to dangerous operating conditions.
Operator Safety:
In environments where heavy machinery and high-pressure systems are in use, the safety of operators is a significant concern. Inadequate pressure control or component failures can result in accidents that endanger workers and damage equipment.
System Instability:
Improperly regulated hydraulic systems can suffer from instability, where pressure fluctuations lead to erratic operation. This can compromise the precision and reliability of the system, increasing the likelihood of accidents or equipment malfunctions.
Minimizing these risks requires robust pressure control and reliable components. This is where mini boosters play a key role in maintaining safe and efficient high-pressure hydraulic systems.
How Mini boosters Enhance System Reliability
Mini boosters are designed to enhance the reliability of hydraulic systems by providing precise control over hydraulic pressure. They help ensure the system operates within safe limits, reducing the risk of component failure and system instability.
Precise Pressure Regulation
Mini boosters can operate in a wide temperature range, from -30°C to 100°C (-22°F to 212°F), depending on the seals and materials used. This makes them suitable for extreme environmental conditions.
Mini boosters are engineered to deliver consistent pressure amplification based on the input pressure they receive. This eliminates the risk of pressure spikes or sudden drops, ensuring that the system maintains a stable operating pressure and reduces stress on critical components like valves, hoses, and seals.
Durability and Robust Design
Mini boosters are built from high-quality materials designed to withstand the demands of high-pressure environments. The hydraulic pistons and cylinders within the mini booster are made from durable metals that resist wear and corrosion, ensuring long-term reliability. This durability reduces the frequency of maintenance and replacements, further enhancing the safety and reliability of the system
Mini boosters are known for their low maintenance requirements, as they contain fewer moving parts than traditional pressure pumps or intensifiers. This increases their durability, with many units lasting 10+ years in operation with minimal service needs.
Pressure Amplification Without Excessive Energy Use
Another key feature of mini boosters is their efficiency. They amplify pressure without requiring significant increases in input power. This means that the hydraulic system can achieve the desired high-pressure output without overburdening the energy supply or causing unnecessary strain on the system. The result is a more efficient system that operates at peak performance without risking component failure
Mini boosters help reduce overall energy consumption in hydraulic systems by allowing high-pressure tasks to be accomplished with smaller, more efficient systems. They can reduce energy use by up to 30%, depending on the system configuration.
Safety Features and Benefits of Using Mini boosters
Mini boosters offer several safety features that make them an ideal choice for high-pressure hydraulic systems:
Built-In Pressure Relief Mechanisms
Mini boosters often come equipped with pressure relief valves that prevent the system from exceeding its safe operating limits. These mechanisms automatically release pressure if it rises too high, protecting the system from overloading and preventing dangerous situations like component rupture or fluid leaks.
Pressure Amplification Without Excessive Energy Use
One of the standout features of mini boosters is their compact size. Unlike traditional hydraulic systems that require large, bulky components to achieve high-pressure amplification, mini boosters can be easily integrated into tight spaces. This compactness reduces the risk of component failure due to space constraints, as the smaller size places less strain on the system’s infrastructure
Mini boosters are compact and lightweight compared to traditional pressure amplifiers. They typically weigh between 1 kg (2.2 lbs) and 15 kg (33 lbs) depending on the model.
Improved Response Time and Pressure Control
Mini boosters provide precise control over hydraulic pressure, allowing for rapid adjustments in response to changing conditions. This is particularly important in dynamic environments where pressure needs to be fine-tuned in real-time. The improved response time reduces the risk of accidents or system damage caused by delayed pressure changes.
Adherence to Industry Standards
Many mini boosters are designed to meet or exceed industry standards for hydraulic components. This ensures that they are suitable for use in safety-critical applications and comply with regulations governing high-pressure systems. Engineers can trust that mini boosters have undergone rigorous testing and certification processes, giving them confidence in the safety and reliability of the systems they design.
Mini Boosters in Safety-Critical Applications
Mini boosters are commonly used in safety-critical applications where high-pressure performance is essential. Here are a few examples:
Aerospace
In the aerospace industry, hydraulic systems must operate flawlessly under extreme conditions. Whether it’s actuating landing gear or controlling flight surfaces, reliable pressure amplification is critical. Mini boosters provide the precise control needed to ensure safe and smooth operations in the air and on the ground.
Automotive Manufacturing
In automotive manufacturing, particularly in the production of high-performance vehicles, precision hydraulic systems are used for tasks such as metal stamping, injection molding, and robotic assembly. Mini boosters ensure that hydraulic systems maintain consistent pressure, reducing the risk of manufacturing defects and enhancing safety on the factory floor.
Offshore Drilling
Offshore drilling operations rely heavily on hydraulic systems to control equipment in high-pressure environments. Mini boosters play a crucial role in amplifying hydraulic pressure for drilling equipment, ensuring that it operates safely and effectively even in the harshest conditions.
Remote Operated Vehicles (ROVs)
These vehicles operate in challenging, deep-sea environments where high-pressure hydraulic systems are critical for controlling movement, tools, and equipment. The compact size and reliability of mini boosters make them ideal for ROVs, ensuring efficient operation under extreme underwater pressures while reducing energy consumption and minimizing wear on components.
Best Practices for Incorporating Mini boosters into Hydraulic Systems
When integrating mini boosters into hydraulic systems, engineers should follow best practices to ensure optimal performance and safety:
Selecting the Right Mini Booster
Choosing the appropriate mini booster for a specific application is critical. Engineers must consider factors such as the required pressure amplification, fluid compatibility, and system load capacity. Selecting a mini booster that matches the system’s specifications will ensure reliable and safe operation.
Integration with Existing Systems
Mini Boosters can be integrated into existing hydraulic systems with relative ease, but care must be taken to ensure proper installation. Engineers should verify that the mini booster is compatible with other system components and that all connections are secure and leak-free.
Regular Maintenance and Inspection
To maintain long-term reliability, mini boosters should be inspected and maintained regularly. This includes checking for signs of wear, ensuring that pressure relief valves are functioning correctly, and replacing any worn components. Regular maintenance will help prevent system failures and prolong the life of the mini booster.
Key Takeaways
Mini boosters play a vital role in enhancing the safety and reliability of high-pressure hydraulic systems. Their ability to amplify hydraulic pressure in a controlled and efficient manner makes them indispensable in industries where safety is paramount. By providing precise pressure regulation, durability, and built-in safety features, mini boosters help engineers design systems that can withstand the rigors of high-pressure environments while minimizing the risk of failure.
As technology continues to advance, mini boosters will likely become even more integral to the design of hydraulic systems, offering engineers the tools they need to create safer, more efficient, and more reliable machines. Whether in aerospace, automotive manufacturing, or offshore drilling, mini boosters will remain at the forefront of hydraulic system innovation, ensuring that high pressure environments are as safe as they are powerful.
Del Rey Partners is the authorized distributor for miniBOOSTER® hydraulic pressure solutions. For more information or inquiries, please contact us at sales@delreypartners.com.